Features
- High Quality Thickness Measurement Location (TML) Labels for Pipe and Equipment Process Safety Management
- Low-Leachable, High-Strength Adhesive
- Temperature Resistance -40°F to 300°F (-40°C to 149°C)
|
Standard Label Product Descriptions
Label A - Measures 3" x 3.875" with a 1.25" diameter opening for inspection and blank spaces for on-site inscription. A UV laminate is an integral part of the label with a removable tab to overlay the inscribed marking. The standard label is bright orange. Wording: DO NOT REMOVE, NDT INSPECTION POINT.
Label B - Measures 3" x 2" with blank spaces for on-site inscription. A UV laminate is an integral part of the label with a removable tab to overlay the inscribed marking. The standard label is bright orange. Wording: DO NOT REMOVE, NDT INSPECTION POINT.
Label C - Measures 1" x 2" with a 0.75" diameter opening for inspection and a blank space for on-site inscription. The standard label is bright orange. Wording: DO NOT REMOVE, NDT PT.
Label D - Identical to Label C with a UV laminate supplied as an integral part of the label with a removable tab to overlay the inscribed marking.
Label E - Measures 1.5" in diameter. The standard label is bright orange. Wording: TML LOCATION, DO NOT REMOVE.
Label E2 (Not Pictured) - Identical to Label E in size, color and wording, but the label stock is 1.8 mil destructive vinyl with UV cured ink. Note: Maximum continuous use temperature is 200°F (93°C).
Label F - Measures 1.25" in diameter with a 0.75" diameter opening. The standard label is bright orange. Wording: UT LOCATION, DO NOT PAINT.
Label H - Measures 1.5" x 1.5" with a 0.625" diameter opening and a blank space for on-site inscription. A UV laminate is an integral part of the label with a removable tab to overlay the inscribed marking. The standard label is bright green. Wording: DO NOT PAINT, NDT POINT.
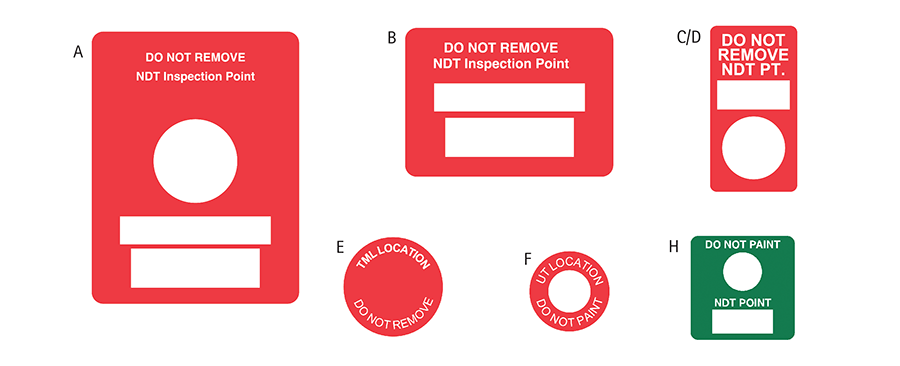
General Product Specifications
The typical label stock is 3.5 mil matte silver mylar polyester material with a 1.0 mil UV laminate. The matte coating resists degradation from scuffing, chemicals, moisture and wide temperature fluctuations.
The adhesive back is a high performance acrylic for strong bonding on textured surfaces.
Leachable chloride, fluoride and sulfur in the adhesive, as measured by ion chromatography - PPM - is 3, less than one, and less than one, respectively.
General Product Applications Guidelines
Minimum application temperature for the adhesive is 58°F (15°C). For best bonding conditions, application surface should be at room temperature or slightly higher.
For maximum bond strength, the surface should be clean and dry. The application surface should be free of loose particulates, such as dust, dirt or corrosion. A typical cleaning solvent is heptane or an industrial grade isopropyl alcohol.
Consult the Manufacturer's Material Safety Data Sheet for proper handling and storage of solvents.
The acrylic adhesive requires 48 - 72 hours to achieve 90% if its ultimate bond strength. Several weeks are required to achieve 100% of its ultimate bond strength. Higher initial bonds are achieved through increased rub down pressure.
Accessories
- Custom design labels (color, size and materials) and metal tags can be quoted
- Industrial strength permanent markers for inspection plugs, labels and tags are available.
|